HABD: On-board Hot Axle Box Detection
A SIL 2 on-board HABD (Hot Axle Box Detection) System that enables continuous monitoring tailored to specific train characteristics, triggering alarms for temperature deviations and ensuring timely safety measures.
Suitable for new builds and train refurbishments, HABD can be used with a TCMS from any vendor


HABD: A Critical Safety Measure for Rolling Stock
HABD, also known as a Hot Journal Detection System, plays a crucial role in preventing serious safety incidents. Bearing failures in rolling stock pose significant risks, including derailment or fire. An increase in bearing temperature is a strong indicator of impending failure, making temperature monitoring an essential predictive diagnostic tool for identifying at-risk bearings before they fail.
Key Differences between onboard and wayside (trackside) monitoring
In understanding the options for Hot Axle Box Detection (HABD), it is important to compare onboard and wayside (trackside) monitoring systems, even though EKE-Electronics specialises in onboard solutions. By examining the differences, we can highlight the unique advantages of onboard HABD systems in delivering continuous, real-time monitoring tailored to the specific characteristics of each train. This comparison helps emphasise why onboard monitoring provides enhanced reliability, faster response times, and greater integration with existing train control systems.
Onboard Monitoring
Standard:
EN 15437-2
Measurement Method:
Sensors inside the axle box continuously monitor temperature.
Data Collection:
Continuous real-time monitoring.
Customisation:
Adaptable to train types, bogies, and bearings.
Detection Accuracy:
Detects gradual temperature changes for early intervention.
Limitations:
Requires onboard installation and integration. Onboard sensors rely on train power and require data transmission infrastructure for real-time monitoring and reporting.
Wayside (trackside) Monitoring
Standard:
EN 15437-1
Measurement Method:
Trackside detectors measure temperature when the train passes.
Data Collection:
Single-point measurement when passing.
Customisation:
Generic system for all trains.
Detection Accuracy:
Only identifies issues when a train passes.
Limitations:
Does not detect issues between detector locations and is not able to detect internal axle box issues.
Build HABD using the following modules
Click on an image to explore related content.
Modular Concept
Below is an example of an HABD system made up of a selection of common modules. The modules are the minimum required for HABD, with additional modules available for expanded functionality. For example, ASDO is often integrated within the same system. Hover over each area to view a brief description or click to access the full module page. Hover over each area to view a brief description or click to access the full module page.

Digital Input Output Module (DIO)
Receives digital signals through its input channels and delivers them to the train computer's central processing unit (CPU) module for processing.
PT100/PT1000 Temperature Sensor Input Module (PTI)
Used to acquire signals from the temperature sensors and convert them into temperature values expressed in degrees Celsius.
CPU with Serial Links (CPS)
A central processing unit providing serial communication interfaces.
Power Supply Unit for VME (PSV)
Provides power for the system.
Vehicle Identification Unit (VIU)
Provides an interface for the Electronic Serial Number.
Application Software
The HABD application software is built on an open-source Linux platform and is coded in C and C++.
Unlike our TCMS platform, which allows users to code their own applications, HABD application software is built by EKE-Electronics. This protects the SIL 2 certification, which requires tools, processes and knowledge about how to produce SIL Safety applications.
How does HABD work?
The Hot Axle Box Detection system is an essential safety feature in railway operations, designed to monitor and prevent overheating in axle boxes and gearboxes. The system operates through a series of precise steps:
- Temperature sensors: Sensors measure the axle box and gear box temperatures.
- Calculate average temperature: The temperature is measured ten times per second. The ten second average is used for calculation.
- Assess the temperature level: The temperature is assessed to determine if it has crossed one of the four thresholds.
- Alarm or action: A notification is issued if the temperature has exceeded one of the four thresholds, either giving an alarm or to undertake a given action, such as triggering the train’s emergency stop.
HABD Key Features
HABD enhances safety, reliability and operational efficiency in railway operations, giving confidence in the monitoring system and ensuring the uninterrupted flow of rail traffic.
The system is equipped with preset temperature ranges, automatically triggering an alarm if deviations occur. This enables timely interventions to prevent accidents or disruptions.
In addition to alarms, the system can take immediate actions, like triggering the train’s emergency stop. Taking immediate action not only prevents potential accidents but also minimises disruptions to rail operations.
Configurable alarm levels are essential to enable tailored safety responses that enhance train operations. Operators can set specific temperature thresholds based on various factors like train types, bearing properties, and operational conditions.
Customising these levels allows the system to accurately detect abnormal temperature rises, signalling potential bearing failures. This optimisation ensures each train receives appropriate monitoring and intervention, thus enhancing safety and reliability across diverse rail networks.
The Hot Axle Box Detection system is a fully redundant system ensuring the highest level of reliability and safety in railway operations. Redundancy involves incorporating multiple independent sensors and backup components that continuously monitor the axle box temperatures.
In the event of a sensor failure or any other malfunction, the redundant system seamlessly takes over without interrupting the monitoring process. This setup guarantees that there is no single point of failure, significantly reducing the risk of undetected issues.
Why Choose EKE-Electronics for your HABD?
The on-board Hot Axle Box Detection system offers real-time, configurable solutions for different train types and designs. With over 1,800 HABD systems installed, you can rely on our extensive experience and trusted performance to ensure optimal safety and efficiency for your fleet.
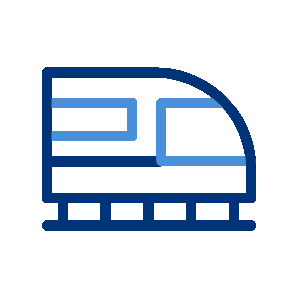
On-board continuous temperature monitoring for hot axle boxes provides superior bearing condition insights over traditional trackside equipment. Unlike intermittent trackside measurements, on-board systems deliver constant real-time data. Monitoring both wheel and gearbox temperatures offers a comprehensive view of axle health, allowing early failure detection and improved safety.
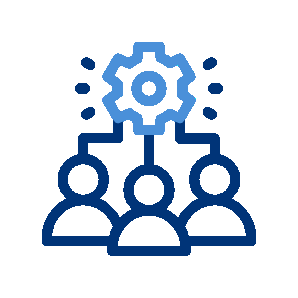
Unlike traditional wayside detection methods, which are limited to monitoring axle boxes located on the outside of the wheels, the system integrates into the train itself, ensuring comprehensive surveillance of all axle points. This ensures that potential issues, such as overheating, are detected immediately, regardless of axle box location, reducing the risk of costly equipment failures, minimising downtime, and safeguarding your operations.
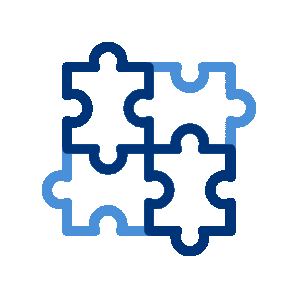
Our monitoring system’s versatile sensor compatibility and flexible configuration allow precise customisation to meet unique customer needs and operating conditions. This approach improves detection accuracy and effectiveness. It accommodates various train models, bogie designs, and bearing properties, providing an efficient solution for railway operators.